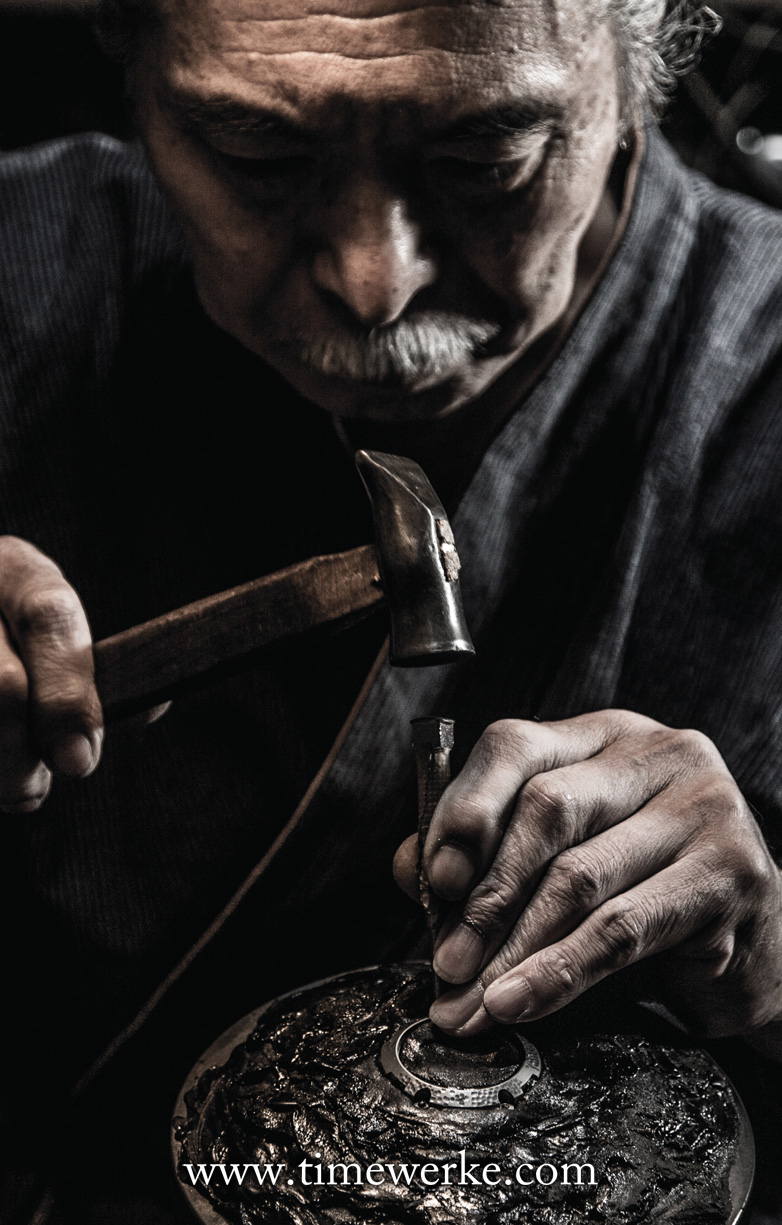
Casio’s G-Shock MRG-G1000HT is literally hammered as it features a traditional Japanese metal hammering technique called tsuiki. This metalworking technique, performed by master craftsman Bihou Asano, is used to decorate the bezel and parts of the G-Shock MRG-G1000HT’s bracelet. Photo: © Casio.
One key highlight from Casio in 2016 is the MRG-G1000HT, a commemorative piece for the 20th anniversary of its MR-G (1996 to 2016), the first G-Shock with a metal case and bezel.
What is interesting is the method of decoration – the use of tsuiki, a traditional Japanese metal-hammering technique on the bezel and parts of the bracelet.
What is tsuiki? Tsu-i-ki or tsuiki is a 1,200 year-old metalworking technique originating from Kyoto, according to Casio. It involves hammering a sheet of metal with metal and wooden hammers till it is thin and what results is a textured relief.
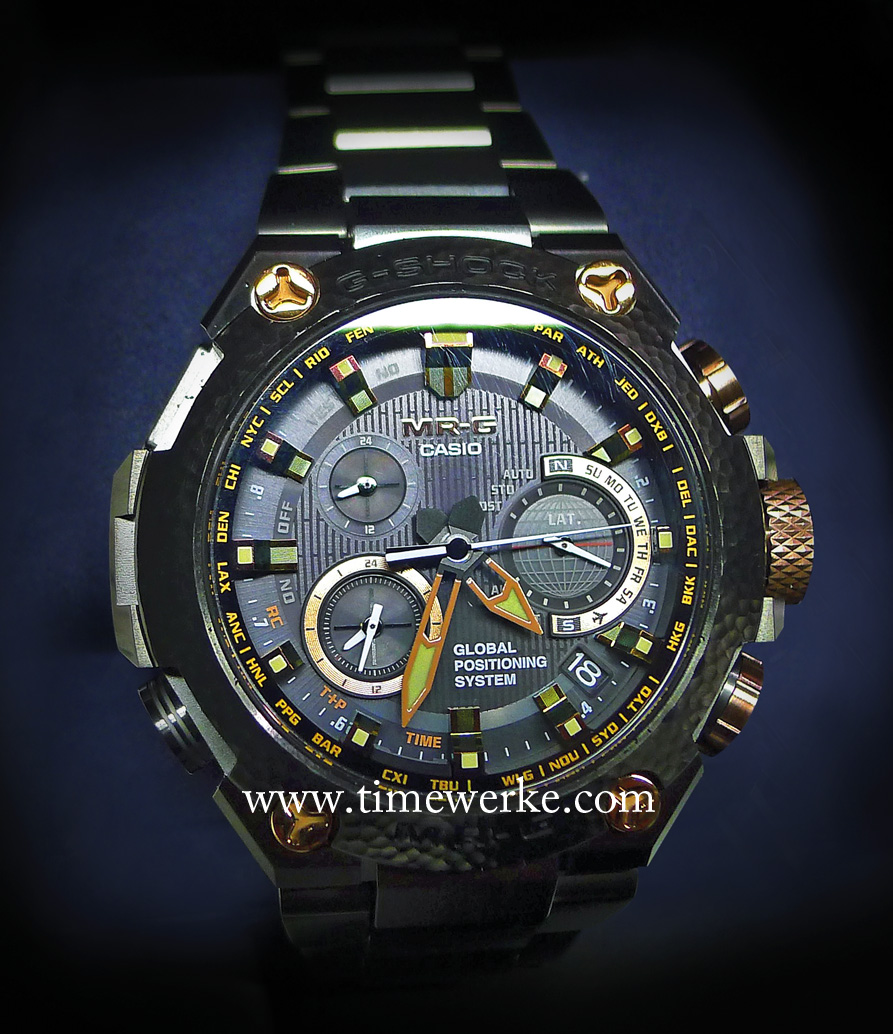
Casio G-Shock MRG-G1000HT Tsuiki Hammer Tone 20th Limited Edition. This G-Shock commemorates the 20th anniversary of the first MR-G (1996 to 2016). Among other things, this MRG-G1000HT features a solar power system (solar-charging system), is able to receive GPS signals and radio wave signals for time calibration and has a world time indication (27 cities with 40 time zones). Limited to 300 pieces and priced at US$6,200 / SGD8,888. Photo: © TANG Portfolio. BaselWorld 2016.
In the past, tsuiki was used to make copperware and different types of metal containers, including armour and helmets. These products required a thin metal that was also strong.
Today, tsuiki is used to produce components for rail cars and aircraft, among other things.
Through a collaboration with Bihou Asano, a third-generation master craftsman skilled in tsuiki metalworking, Casio’s MRG-G1000HT showcases this traditional metalworking technique.
In Japan, Asano is well-known for creating and restoring suspended incence burners for the Kyoto State Guest House and rooftop statues of deities for the Osaka City Central Public Hall. His skills have allowed him to restore artworks classified as “Important Cultural Properties” in Japan.
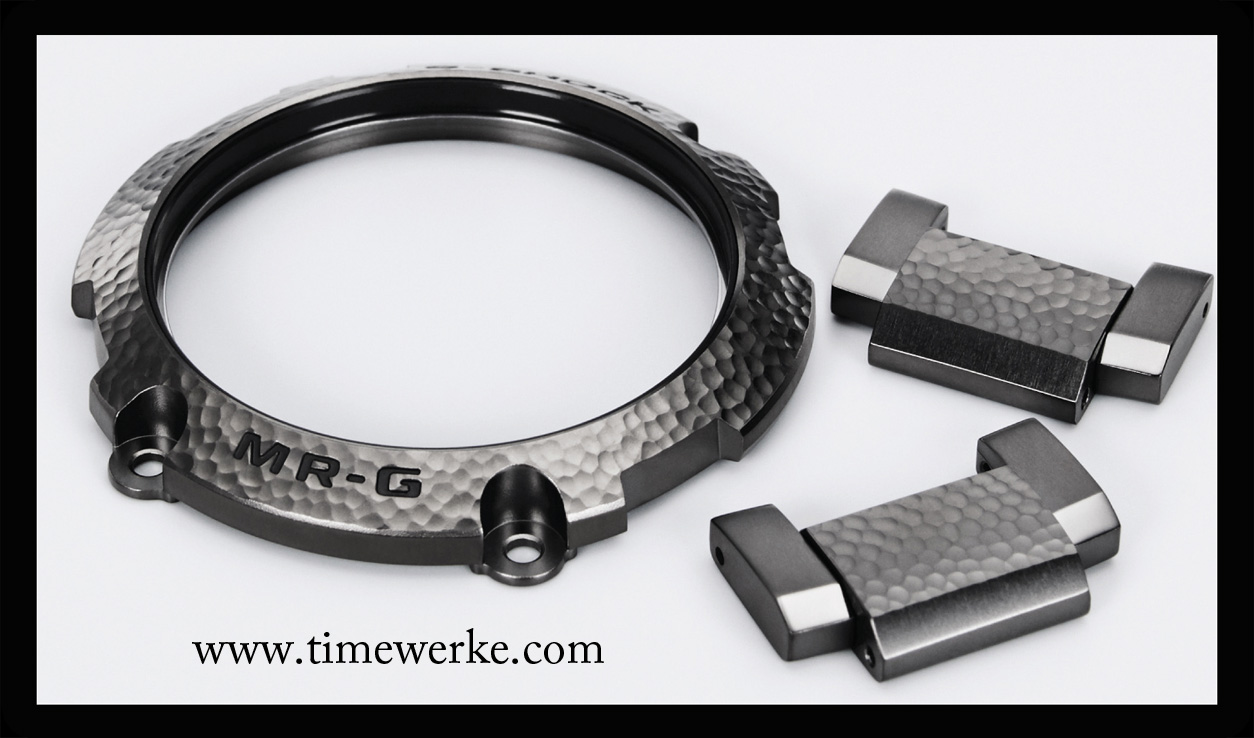
The hammer tone finish is used on the bezel and parts of the titanium bracelet. This explains why the G-Shock MRG-G1000HT is nicknamed the “Tsuiki Hammer Tone”. Photo: © Casio.
Using the tsuiki technique and with its hammer tone finish on the bezel and parts of the titanium bracelet, it is little wonder why Casio’s MRG-G1000HT is also nicknamed the “Tsuiki Hammer Tone”.
What must be highlighted is that tsuiki is typically used on copper sheets. For Casio’s G-Shock MRG-G1000HT, tsuiki is performed on titanium, the material of its bezel and bracelet.
Titanium is a much more difficult material to work on and as such, only parts for a total of three pieces of the Casio MRG-G1000HT can be made a day.
Having the tsuiki hammering technique as a feature on the bezel is apt. After all, the bezel was the basis for which a solution was found by Kikuo Ibe and his team to allow a metal case to be used for the first time on a G-Shock watch – the MR-G that was introduced in 1996, also known as the Metal Version G-Shock MR-G 100.
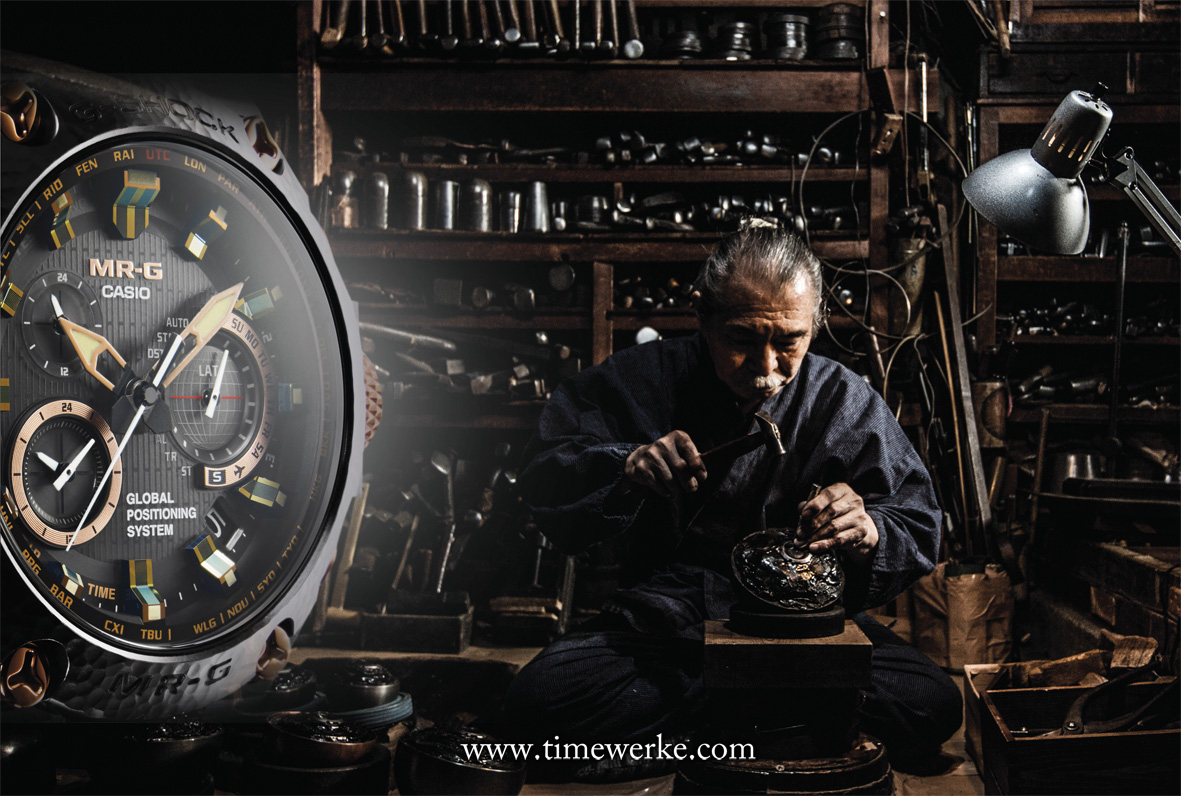
Born in 1943, Bihou Asano is the Japanese artisan who used a 1,200-year old technique to decorate the bezel and parts of the bracelet of the Casio G-Shock MRG-G1000HT using the tsuiki technique. Photo: © Casio.
“The bezel damper protection was inspired by the bumpers of cars and we used rubber inside the case,” Ibe explains. The bezel is the part most prone to shocks. It was therefore created as a separate component, allowing rubber shock-absorbing material not only to be placed in between the bezel and the case, but using it as a cushion between the bezel and the glass.
The water-resistance of the G-Shock MRG-G1000HT is 200 metres. “Right from the beginning, our G-Shocks were twenty-bar water-resistant,” notes Ibe.
Another related Casio article on timewerke.com that may be of interest is:
i. Casio G-Shock MRG-G1000HT Hammer Tone: Traditional Japanese art